全模分析
模具网格装配模块
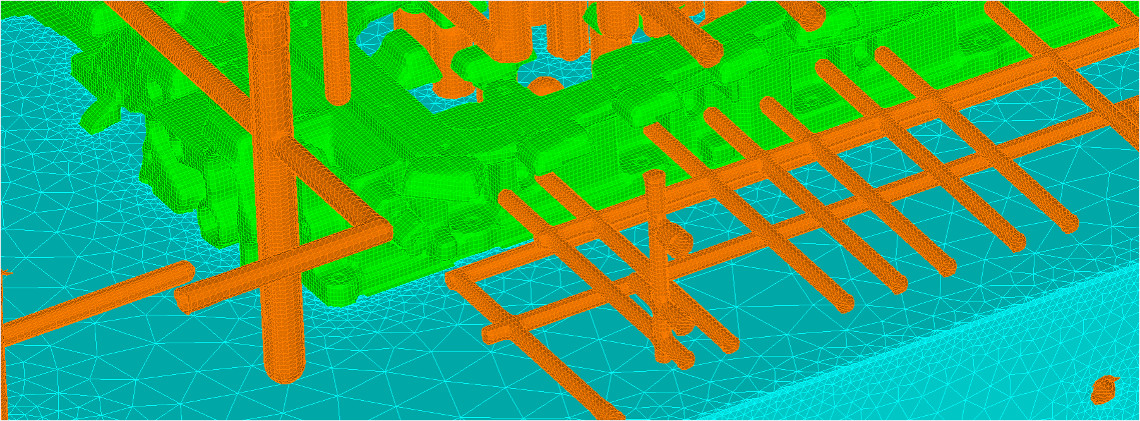
Cast-Designer 支持混合网格技术。四面体网格用于模具以节省元素数,而六面体网格用于铸造以保持良好的流动效果。即使在不同的网格类型中,接触节点的位置是相同的,以满足热传的需求。
网格技术综述
Cast-Designer 的网格装配模块,用于把复杂的3D CAD模型,转换为网格模型,能够正确处理铸件,模具,顶针,水路,型芯等对象,支持高压铸造,金属型铸造,低压铸造等不同的工艺。全模网格装配过程无需手动干预,全自动进行,使用简单,节约90%的人力时间。整合多种创新的网格技术,包括网格重划分技术(Re-Mesh),粗化网格技术,网格投影匹配技术以及自动驱动技术等。
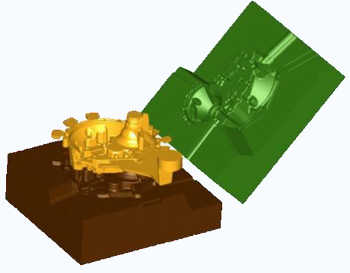
CAD 全模数据
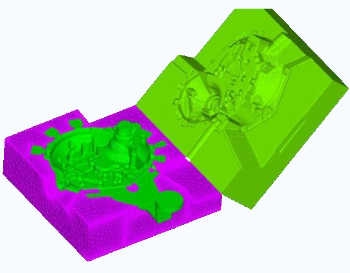
全模网格装配15分钟
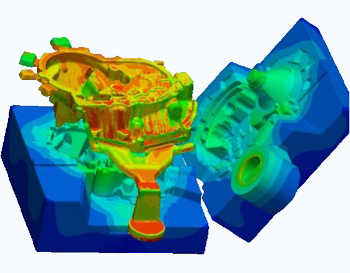
铸件与模具温度
混合网格: 节约90%的时间
在模具温度循环模拟,以及热平衡模拟中,精确的模具几何表征对于计算至关重要。
- 铸件采用六面体网格划分,可以获得更好的流动计算结果
- 模具采用四面体网格技术,有利于热计算和机械应力计算,计算效果稳定快速,能够支持较大的网格梯度(网格大小过度比例)
- 网格匹配的难点在于,不同元素类型的界面处节点的连续性(铸件和模具的接触面上)Cast-Designer 能够很好的自动处理这样的过渡连接
- 相对传统方法,网格处理速度高10倍以上
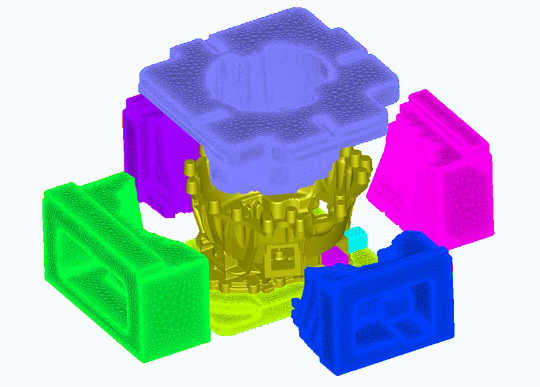
低压轮圈铸造模型
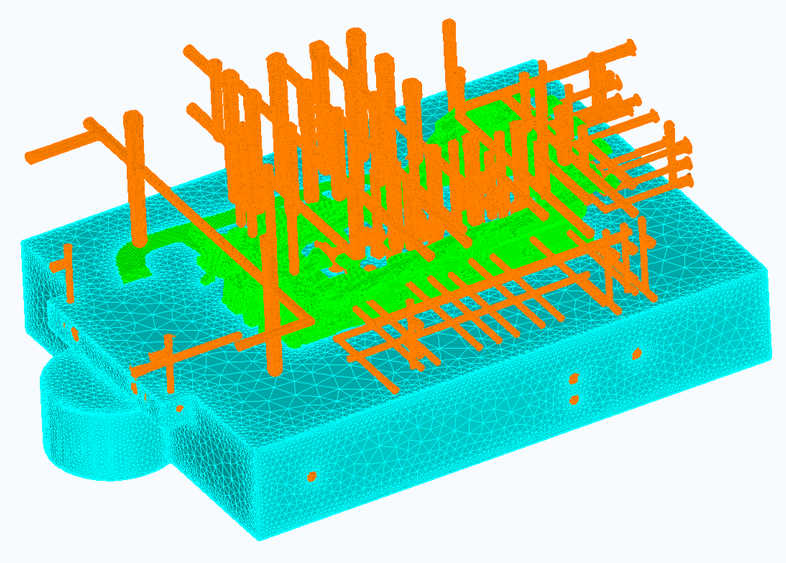
高压铸造模型含水路
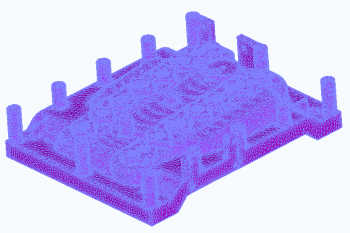
上模: 721,320 单元, 195,099 节点 (四面体单元)
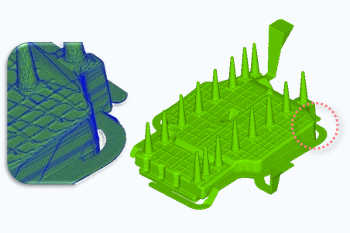
铸件: 436,679 单元, 604,052 节点 (六面体单元)
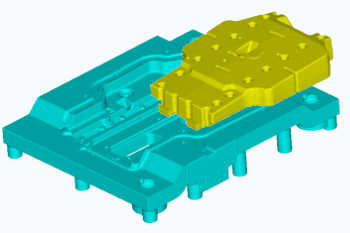
砂芯: 776,328 单元, 203,632 节点 (四面体单元)
底模: 976,940 单元, 259,331 节点 (四面体单元)
重力金属型铸造模
全模分析与循环模温计算
Cast-Designer 提供了循环生产周期的模拟能力。
支持影响热流和模具热平衡的所有重要参数的定义。
支持生产周期全过程的综合定义。
- 顶出时间(由时间或浇铸温度控制)
- 开模顺序(作为时间的函数)
- 延迟时间(模拟循环中对热平衡的影响)
- 合模顺序(如时间和温度的函数)
- 等待时间直到下一个周期
- 可以模拟不同等待时间的不同结果
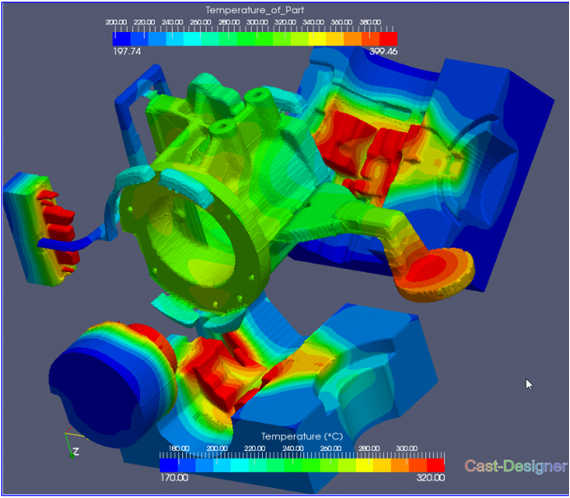
模具与铸件在多个生产周期后的温度场
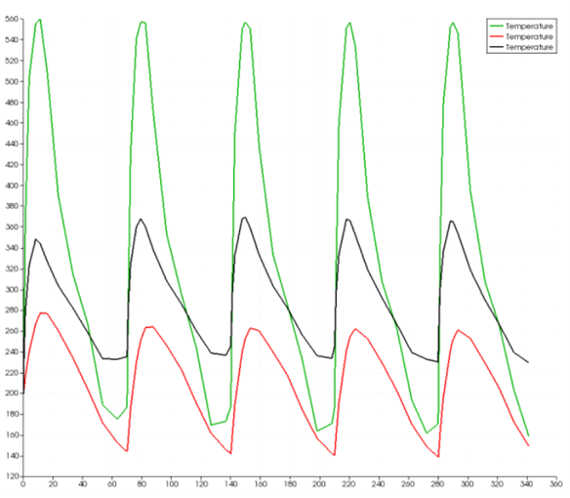
循环温度模拟的热平衡曲线
模具冷却与温度计算
- 支持模具冷却与加热管道的全面考虑
- 每个冷却或加热管道均可独立控制
- 管道控制可以依赖于时间或者温度
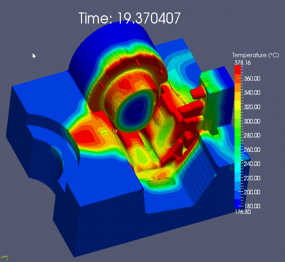
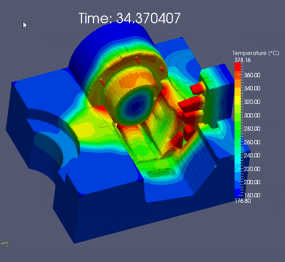
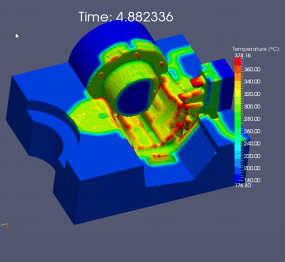
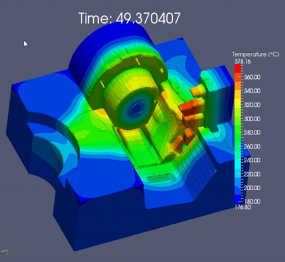
完整生产周期中的模具表面温度场分布